連載コラム『Jコスト改革の考え方』目次
JBpress連載コラム『本流トヨタ方式』
ビジネス情報サイトJBpressにおいて、2008年から2013年までの間に合計104回のコラム 『本流トヨタ方式』 を連載していました。
現在連載中のコラム 『Jコスト改革の考え方』と併せて読んで頂くと、より深くJコストの考え方がご理解頂けるかと思います。是非、下記のリンクにアクセスしてみて下さい。
過去の所信表明
2017年8月
『現地現物』の私的『原体験』
今回は 『現地現物』の私が経験した 『原体験』をお話しします。
今年は2017年、私がトヨタに入社したのが1967年ですので正に50年過ぎたことになりますが、トヨタで過ごした33年間、ものつくり大学での7年間、その後コンサル会社を興しての10年間の活動を支えてくれた一つの柱は、今からお話しします 『現地現物』の 『原体験』によるものでした。
『原体験』その1
入社教育後行われた2ヶ月間の『現場応援』
新入社員教育でも2週間×4職場の 『現場実習』がありましたが、それはあくまでも現場作業の体験が狙いで、作業量は1人工分の一部に過ぎませんでした。
しかし、 『現場応援』は1人工としてカウントされた要員ですから、その本質は全く違っていて、一刻も早く一人前にして仕事をしてもらわなければなりません。それは正に 『期間工』として採用された人がトヨタの現場でどう扱われて、どう一人前に育てられるかの 『体験コース』でもあったわけです。この時の体験が、私のライン作業に対す考え方の基礎になりました。
その時に学んだことの幾つかを紹介しましょう。
-
『コンベア作業』は下りのエスカレーターで2階に上がろうとしているようなもので、昇っても、昇っても、階段は降りてくる繰り返しで、変化が欲しくなります。
部品箱が空になり、入れ替えるのが楽しみになります。
単一車種生産より 『多車種混流生産』の方が変化があって楽しいのです。 - 部品とボデーの精度が合わず、調整しながら取り付けなければならない時、リズムが乱されるので腹が立ちます。
- 作業の中に課題を見つけ、工夫しながら作業をするとゲームのようになり楽しくなります。 『KAIZEN』の意味が分かってきます。
-
『難しい作業』ほど、やり甲斐が出て来るし、来るのが待ち遠しくなるります。
他人の出来ない作業が出来る事が何よりのプライドになります。 - SPS(部品セット供給)は自由が奪われるので、 『ありがた迷惑』、時間をもらって自分でPickingした方が楽しいし、作業姿勢の変化が付けられて身体に優しい。
- 作業中にLeaderが廻ってきて声を掛けてくれるのが嬉しかったし、気分転換してこいと言って、5分間ぐらいずつ1日数回作業を代わってくれるのが特に嬉しい。
- 締め付け工具の操作に慣れて、ベテランと遜色ない速さで作業が出来るようになった事や、締め付け音を聞いて正否が判別できるようになった事が大きな財産となりました。
これらが身についたお陰で、私自身が設計と作業性について談判できるようになりましたし、現場の仲間として受け入れられるようもなりました。
私のこの経験から、工科系大学出身者を1人前の技術者に育てるためには、ある期間を限って 『一工員として現場体験させること』をお薦めします。
『原体験』その2
『管理能力向上プログラム』の代筆経験
当時のトヨタを社内体制から見ると、1965年デミング賞、1970年デミング賞実施賞を受け、強化を図りましたが、約10年経過した1979年には、受賞当時の部課長が定年を迎え、 『管理能力の劣化』が懸念されるようになりました。
その一方でトヨタを取り巻く環境は、
1970年まで1ドル360円でしたが、1971年のニクソンショックを経て1978年には1ドル176円に急騰してしまっていました。
1973年に起きた第1次石油ショックで原油価格は約20倍にも高騰し、その後下がってきたものの1979年には第2次石油ショックが起きます。又1980年からは本格的な排気ガス規制も始まる・・・という極めて厳しい情勢を迎えていました。
これに対処すべく、1979年1月から部次長を対象として 『管理能力向上プログラム』が開始されました。
具体的には 『工場長方針』を受けて定めた 『各部長方針』の中の最重点項目を取り上げ、その具体的な 『展開状況』 『進捗状況』を 『A3用紙』1枚に纏め、 8分間で理路整然と分かり易く 『役員』に説明せよ・・・というものでした。
上司であるM部長は当時係長であった私にこれをマル投げしてくれました。
字が上手な部下と2人で苦心惨憺して手書きで完成させ、レクチャーして発表会場に送り込みました。発表の場でM部長が受けた『御指導』は増幅してお叱りの言葉としてM部長から告げられ『出来の悪い部下を持つと苦労する』と嫌みまで言われましたが、係長の分際で部長教育をして頂いた事は、私にとっては大変貴重な体験でした。
『現場応援』と 『管理能力向上プログラム』の 『原体験』が 『現地現物』即ち 『現場』に出掛け 『現物』を観察し、 何故?何故?・・・としつこく追求し 『真因』を探り当て対策するという 『行動規範』を作る基になったと考えています。
改善のお手伝いをしている中国企業の話
ここからは毎月1週間ほど改善のお手伝いをしている中国企業の話です。
現場は最新の設備が設置してあり、欧米Makerの基幹システムが導入され、Officeでは事務職員がDisplayとKeyboardを前に黙々と働いていました。ところが現場には在庫の山があり、一方では欠品があり、とても有名な基幹システムの成果とは思えないので、得意の 何故?何故?を中国人にぶつけました。
その結果、驚くべき事に、誰も基幹システムのLogicを知らず、部品が納入されてもその日のうちに入力すれば良いと考え、帰り間際に纏めて入力していました。Supplierへの納入指示は、設計変更があって生産計画から全て再計算して手入力する製品群があり、2〜3日遅れて発注している部品もありました。
中には経営者の親戚だと言って、Keyboardもろくに打てないような人がおり、仕事が遅いどころか、遅れても平気で帰ってしまう始末・・・・でした。
ところで、皆さまの会社は上記の中国の例を他山の石としてご確認をお勧めします。
8月と言えば、本年度の新入社員が入社教育を終え職場配属になる時期でもあります。
製造現場に作業員として配属になる場合の職場教育は、適性検査や、工具取扱の基礎訓練、作業訓練、作業要領書による 『やらねばならない事』『やってはならない事』等を叩き込まれて仕事に就きます。
私の知るかぎり、製造工場ではあるレベルで実施されています。
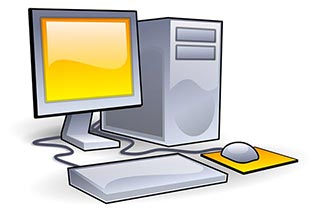
その一方で、殆どの大卒者は事務所にいて、DisplayとKeyboardを相手にしての作業になりますが、御社の大卒新入社員の場合はどんな基礎教育がなされるのでしょうか。
Keyboard操作の基礎訓練は・・・、Computer Literacy はどう把握していますか?基幹システムのLogicは教え込んでいますか・・・・
Displayに表示されているデータは何処でどのようにして計測し、どのようにして入力された、いつのデーターなのでしょうか?
新入社教育のみならず、現在各部書でDisplayとKeyboardでやっている仕事の総点検と、業務分掌の見直しをお薦めします。
特にものづくりの基本中に基本 『生産計画』はどのような基本データーをもとに、誰が、どのようなLogicで立案して、どんな手続きで決定され、どのような速さで展開しているのか?
幾つかの会社で調査しましたが、多くは ノンキャリ社員の勘でやられていました。
2017年7月
今こそ『現地現物』に立ち返るべし
今,日本国中が将棋界の奇跡,藤井聡太4段の快進撃に沸き返っています。
29連勝と言う空前の記録を作り,7月2日には30連勝なるか・・・・将棋ファンのみならず全国民が固唾を呑んで見守って居ます。これを受けてテレビ各局は競って藤井四段のこれまで成長してきた経緯や,日常の努力などの話題を取り上げ,将棋界を代表するような皆様が解説しています。私も引き込まれて見ていました。
テレビを見ながら私は知人から聞いた 『人類は【A】,【B】の二つの能力を身につけることで今日の繁栄を手に入れた』と言う知人の話を思い出しました。以下その受け売りを含めて,今,日本で起きている事への私の懸念をお話ししたいと思います。
【A】人間と人間を繋ぐ能力
先ずその一つであるCommunicationについては,数十万年前の旧石器時代迄遡ります。 この頃人類は幾つかの家族同居の形で洞窟に住んでいた事が分かっています。群れをなして生活し,自分達より強い獲物を狩るためにはかなり高度な意思伝達が必要になります。当時は乏しい語彙と,顔の表情や身振り手振りでお互いの気持や考えを伝え合っていたと考えられています。この状態が数十万年続いたので,表情やしぐさで相手の気持ちを推し測ると言う人類共有の能力を身につけたのでした。
その後各地に散り,独自の言語や風習を身につけていき,集落から国家という大規模な集団を営むようになって行きますが,祖先から引き継いだこの能力があるので,言葉の壁を越えて,演劇が鑑賞され,外国映画が上映されるのだと言います・・・・・・・・・。
【B】人間と自然界を繋ぐ能力
自然界を観察し,獲物を見つける能力,食べ頃の果実を探し当てる能力などを指し,この能力のお陰で人類は生存し続けました。更に進んで動物を飼い慣らして家畜とし,稔っても種子を飛び散らさない植物を発見し,それを栽培する事で大量の穀物を手に入れ,更に布を織り,衣服を作り,家屋を作りました。
やがて太陽や星の動きから?を作り,?に合わせて集落全員で農作業をすることで効率を上げドンドン豊になって行き,人類は文明を作り上げて来たのでした。
この【A】,【B】の能力は誰もが持っていますが,社会の進化に伴い分業化されていき,【A】の優れた人は人々を束ねる仕事である『士』『商』に就き,【B】に秀でた人は自然界の恵を人々が必要とする商品に変えて提供する,『農』『工』を担うようになって行きました。
この分担が定着し,更に細分化・専門化が進むと【A】と【B】の気質も以下のように分かれていきました。
【A】を得意とする人間群(社会科学的)の特徴
会社勤めの殆どの人がこの分類に入りますが,眼前にある『情報』や『学説』の正否よりも,回りの人間関係に一番の関心を持ち,中に溶け込み,同質化することに腐心します。更に能力のある人達は,その人間関係の中でLeader Shipを握るようになり,更にその人間関係を操る事に喜びを感じるようになります。
結果,自社を如何に成長させるかと言ったことより,社内の人間関係に強い関心を持ち,どの派閥に属していた方が有利か,誰のいう事を聞くべきかなどを嗅ぎ分ける事に腐心します。能力のある人は社内に然るべき人脈を構築します。
特に長けた人は社外にも太い人脈を作り上げて居ます。そして一旦社内で解決すべき課題が発生したときには,その人脈を活かして素速く解決してしまいます。それが社内で揺るぎない評価を得,出世街道を上り詰めやがてTopになる場合が多いようです。客観的にも現状維持にはこれは必要なことです。
しかし,その解決法は 『既存の自社の枠組み』の中で行われることなので,市場とのズレから来る問題には,逆に,事態を悪化させてしまいます。
一刻を争う応急処置は 『既存の自社の枠組み』の中で行うとしても,本対策案作成時には 『現地現物』に徹して【B】の人間を使って自社の仕事の進め方と現状の市場との関係を厳しく点検し,半歩先んじて市場をリードできているか否かを確認するところから始めなければ成りません。
この点検を怠ると会社は ガラパゴス化されていきます。
【B】を得意とする人間群(自然科学的)の特徴
人間関係よりも自然現象に強い関心を持ち,眼前にある『情報』や『定説』の正否を気にします。それを確かめようとして一人で観察したり,考え込んだりする性癖があり,これを『変人』とか『奇人』として軽蔑されたりします。
又『他人の心』や『その場の雰囲気』を察することが苦手なので『KY(空気が読めない)』として馬鹿にされたりします。しかし自然現象に対する感性は鋭く,会社において異常を発見して事故を未然に防いだり,品質不良の真因を解明したりするのはこの人達なのです。
更に能力に長けた人は市場の変化をCatchして、 『新商品』を産み出したり,自社の業績を観察して 『経営課題』を顕在化させるなど,会社存続のための最も大切な部分を担う人材として必要な人材なのです。
人物像が想像出来ない方はテレビドラマの『相棒』の 杉下右京や,『科捜研の女』の 榊マリコをご覧ください。両名がそのキャラを良く表現しています。
ここからは,この文脈上で,企業の改革・改善業務に携わっている専門家としての立場から,ここ4〜5年ものづくり現場で私が感じ始めた心配事を御説明します。
【A】が最近抱え込んだ問題
少子化の為,子供達が群れになって遊ぶ中での下級生へのいたわりや,LeaderShipを発揮しての競い合うのを磨く場がなくなり,面と向かって議論し言い負かす機会も消えました。
更にスマホの普及で,隣り合って座っても共にスマホをのぞき込み,ゲームをするか,遠くの同年のメル友と絵文字の通信をする・・・という生活になってしまっています。顔を合わせて交わす会話は「えっ!うそ!ほんと!すげ〜!」で代表されるような語彙の少ない会話。これが10余年前大学で教員をしていた頃の学生達のコミュニケションに対する実感でした。
この学生達の世代が今,会社の実務を担う30代として働いているのです。
【B】が最近抱え込んだ問題
自然界との接点を担う【B】は,もっと大変な事になっています。子育て中の世代は都会暮らしのため,その子供達が大自然を自分の五感で感じる機会が少なくなってしまいました。学校教材の文章や画像で学ぶしかありません。
1990年代になるとインターネットが普及し,検索すればどのような情報も入手出来,項目数は膨大になりましたが,内容は文字と画像には変わりなく,拙いことに誰でも投稿出来るため,『群盲象を評す』と言う印度の寓話通りの情報が溢れているのも事実です。
その一方で,Computerのいわゆる2000年問題が顕在化し,これを乗り越えるために各企業は社内の基幹システムを更新したと言われています。その結果,会社内では営業からの注文情報を入力さえすれば,Computerが「材料発注」「生産指示」「納品指示」等迄やってくれるので, 『現地現物』による確認は全く不要で,各部書はその 「指示」に従って作業すれば良い・・・という状況が20年近く続いていると言う事になります。
社員の年齢から見ると,課長層の中堅以下新入社員に至るまで,入社以来,Display上のComputerからの指示を見て,Keyboardを叩いて回答するという作業しか教えられず,どんなLogicで動いているのか,現場がどうなって居るのか,どんな時間差なのか 『現地現物』で確認できないまま作業している・・・と言う実態があるのです。
以上が,かねてから抱いていた私の懸念です。
最近,この「懸念」が現実となってきました。
マスコミ報道を私流に解釈すれば, 東芝がおかしくなったのは,米国の原発建設会社の 『現地現物』による調査をせず, Display(Computerが出した結論)で判断して買収し,その後もDisplayとKey-boardで対応してきたためで,もっと言えば【A】の人材ばかりで 『現地現物』の出来る【B】の人材がいなかった為と理解出来ます。
タカタの倒産も同様で,ワンマン経営だったと聞いていますが,真因追求し,市場の動きを見極め,場合によってはクビを覚悟で社長を説得する【B】の人材がいなかった為であると言えます。
三菱のMRJの開発遅れも,開発現場で真摯「妙手」を追い求める【B】の人材の絶対量が不足しているためと聞いています。
そんな懸念を抱いていたときに見たのが,
中学生である藤井四段の目を見張る活躍でした!
将棋の世界は,抽象化されて独自のルールがあるモノの,一種の数学であり,正に【B】の世界です。この活躍に刺激されて,小中学生が挑戦し始めたと言います。大変嬉しいいことです。
卓球の世界でも同じく中学生の張本選手が世界の強豪を相手に大活躍をしている様子です。卓球は相手の動きを瞬時に読み,数手先の体勢の乱れを誘う知的スポーツで在ると聞きました。
正に【B】の世界です。彼等が刺激になって【B】の人材が輩出することを願うばかりです。
最後に皆さまにお願いしたいこと・・・
小中学生の諸君は,
人間関係を気にせず,藤井四段や張本選手が頑張っているように, どんな分野でも良いから 『成りたい自分の未来像』を目指してがんばってください。
それが自分を変え,周りを変えていくし,社会が求める人材になって行けます。
何よりもその過程が,皆さんの 『充実した人生』そのものなのです。
現に会社に勤めていて,私の懸念に同感する皆様は,
Displayから離れて現場に行き,関わっている製品を手に取って先ずその質感を味わってください。
次に,Key-boardを叩いて出した現場への指示は,何処に出され,実際にはどんな作業が始まり,どう終わり,終わったらどんな形でそれがSystemに入力されるのか, 『現地現物』で調べ,自社に中で御自分が何をやっているのか・・・を確認して下さい。
それが終わったら,このホームページに連載されている 『Jコスト改革の考え方』 シリーズをお読み下さい。読み終わると,あなたに 『生き甲斐,働き甲斐』を与えてくれる道が見えてくることでしょう。
2017年6月
先月のある夕方,新幹線で名古屋に帰ろうと京都駅に着いたとき,駅の中に大勢の高校生と思われる生徒達が床に座っていました。床に直に尻を付けて座るという経験を持たない私には,その姿に強烈な印象を受けて,本職である「生産」「物流」に関しての思いがこみ上げてきました。
[1]団体客を運ぶ事の難しさ
数百人単位の生徒達を引率することは大変なことですから,分単位で運行する新幹線にJust In Timeで対応することは大変なので,早めに来て待たせるしかないことは理解出来ました。引率する先生方のご苦労が偲ばれます。
受け入れる新幹線側も大変で,ほぼ満席に近い状態で,厳しい定時運行している新幹線に,いきなり1列車に数百人の団体客を乗せたらダイヤも乱れ苦情が殺到するでしょう。常連の客には迷惑を掛けないように時刻表には書いていない団体専用列車を仕立て,定期列車の合間を縫って運行している様子に,流石と思いました。
トヨタ生産方式の立場で説明しますと,新幹線の通常運行は,老若男女分け隔て無く席を準備し,乗車券は1人単位で販売しています。これはトヨタ生産方式が目指す究極の姿,即ち平準化しての『1個流し』に他なりません。その結果顧客は待たずに乗りたい列車の席を確保出来るのです。工場でも,市場の要求し即時に対応出来るのです。
逆に 『平準化』し 『1個流し』が出来ている工場では,大ロットの注文は折角の 『平準化』を 崩してしまうので困るのです。
現に私が現役でトヨタのSupplier改善をしていたとき,アンチトヨタ式の自動車工場から突発的に大ロットの注文が飛び込み,その自動車会社の分は在庫を抱えて対応せざるを得なかった苦い思い出があります。
そのことがあったので,修学旅行客の扱いに感心したのでした。
そして営業関係の方に申し上げたいのは,大量に受注するのは結構なのですが,納品は是非 『平準化』して自社の生産を乱さないようにしてほしいものです。
[2]昔の渡し舟は・・・・
現在の列車は「定時不定量」輸送で,客を待たせない運航ですが,昔の渡し舟では,専用の舟があり,専任の船頭さんが居たのに平気で客を待たせ運行回数を任意に減らして,あたかも「定量不定期」的運用していたようです。
因みにトヨタ生産方式では,運搬の改善とは,1番は橋を架けて運搬を無くすことであり,2番は最大限多頻度で運ぶ事を教えています。この渡し舟で言えば,船頭さんが居て,日当を支払っているのであれば,その船頭さんに目一杯働いていただき,客が一人でも居たならその客を向こう岸に運べ・・・
つまり,客の待ち時間を最小にする事を考えよと教えています。
実際は「舟宿」という言葉が残っているように,渡し場には宿屋や茶屋があり,旅人はしばし休憩を取った後で舟に乗り川を渡った・・・とされています。
その実態は上方落語に,客が舟宿に入って飲食を注文し代金を払い終わった頃を見計らって「舟が出るぞ〜」という呼び声を出させ,飲食を出さずに客を舟に送り,儲けている悪徳舟宿の話がありますが,顧客第1に考えLead-Time短縮居に努力したとは言いがたい時代だったのでしょう。
舟宿を倉庫,渡し舟をトラック業界に置き換えれば現代でも思い当たることがあるような気もします。
[3]生産計画に新幹線方式を採ったら・・・・
毎年,盆・暮れ・5月連休には新幹線の混み具合がニュースになります。時刻表を調べるとそれ以外の季節でもこまめに臨時列車を走らせているのが分かります。多分前年度までの実績をもとに運行ダイヤ(生産計画に相当?)を決め,「切符と言う商品」を売り出して居て,各所にある自動販売機で購入できるような短いOrder-to-Delivery-Lead-Timeで売っている事が理解出来ます。
一般企業で,この新幹線の切符と同じ方式で生産したらどうなるでしょうか?
例えば,1日千台という需要予測に基づいて月間の生産計画を立て,生産の構え(列車のダイヤに相当)を行います。顧客からのオーダーは,何日の何時の列車の指定席といった具合に生産計画を決め,かち会ったら次の列車をお薦めして決めていきます。
これによって顧客に画期的に短いOrder-to-Delivery-Lead-Timeを提供でき,更にこれによって顧客に到着時刻を告げるように,完成時刻をお知らせできます。
一般に予算原価法を採用している会社では,空席があるとその分が赤字になる設定をしますから,顧客のLead-Time要求よりも自社の見かけの利益を追求し,常に満席になるようにダイヤを組もうとします。これが多在庫を抱え資金繰りに苦しむ経営を迫っている元凶です。
新幹線の席のように,工場のコンベア上に例え空席があっても,常にLead-Time最短を目指し顧客の満足を得て市場を掴み高収益で成長する企業を目指すべきだ・・・・イレギュラーな大口商談には,それなりの事前交渉を持ち,修学旅行のように特別列車を仕立てるとか,乗客の絶対量が違うJR東海とJR西日本との間では乗客の利便性(Lead-Time)確保する為に,乗り継ぎ地点では頻度は確保した上で,16両連結を8両連結や4両連結など車両数を減らし収益性を確保している等々,学ぶべき点が多い。
これから「ものづくり経営」は顧客への利便性の向上が必須と思われるが,新幹線が色々示唆を与えてくれる。もっとしっかり勉強しようと車中で考えながら帰途に就きました。
2017年4月
季節のご挨拶
2017年も桜咲く4月となりました。念願の会社に入社された方,職場を異動された方,昇格された方,それらの方々を迎え入れる職場の皆様,新規蒔き直しで,意を新たにして仕事に取り組まれていると思います。心からエールをお送りします。
某国の議会では宰相が本人及びその夫人に対し『 忖度がなかった』と大見得を切り,マスコミを賑わしていますが,この事は『他山の石』として学ぶことが多くあります。
例えば,普段何気なく「名古屋の『ういろう』は美味しいね」と口にしていれば,名古屋に出張した部下は,報告時に「ういろう」の土産を差し出すでしょう。これは,部下が上司にする 忖度です。突っ返せば部下が傷つきます。「気を遣わせて悪かったね」といって受け取ることでしょう。これは上司が部下にする 忖度です。
この事を,業務の標準化という観点から見れば,「出張に土産は不要」というルールがない故に起きた事態と考えるべき事柄なのです。
次に,昇格した方が心すべき「上に立つ者の言動」という観点からは「帝王学」というテーマがあります。帝王学といえば,昭和天皇は大相撲が大好きでしたが贔屓力士は口外しませんでした。園遊会等では労をねぎらったお言葉に御返事差し上げた内容に対して『あっそう』としかお答えにならなかったことも有名です。並んでいる参加者1人ひとりに平等に接するには『あっそう』と答えるしかなかっただという解説を聞いた事があります。
上司は仕事では部下に厳しく接する一方で,個人としては平等に接することが大切で,お追従が通用するような職場関係を作ってはならないという事でしょう。トヨタでは 『やらねばならない事とやってはいけない事の二つしか無い』と教えられ,それを明示したモノが 『表準作業』であると教えられてきました。現場でも事務所でも,状況に応じてやったりやらなかったりすることに根源的な問題があるのです。
最後に,異動で新職場に行くと『あれっ!?』と思う業務や慣習にぶつかることがあるでしょう。その時,『郷に入れば 郷に従え』と疑問点をぶっつけず黙って従うのも『 忖度』のうちと思います。『おかしい』と思ったことは言葉に出し,納得いくまで議論し,職場を変えるというのも,定期異動の効用なのです。『石の上にも3年』という言葉は冷たくて座り心地の悪い石の上でも年月が経てば居心地が良くなってしまい,課題が見えなくなってしまうという警鐘を意味しているのです。
先日,小泉農政部会長が,東京オリンピックの選手食堂に提供できる日本産食材はGAPの認可を受けていないため1%にも満たない・・・・という発言をしました。日本の農政関係者がロンドン大会から実施されていた規約の国内展開を怠った為に起きた事態でした。このように部下が上司の顔色を窺い『 忖度』すれば組織はガラパゴス化してしまうのです。
新規蒔き直しのこの時期に『 忖度』を我が事として職場の点検をお勧めします。
2017年2月
2017年度の取り組みについて
いよいよ米国ではトランプ政権がスタートし,TPP離脱,NAFTA再交渉,国境に壁を作る等の大統領令に署名したとの報道がありました。欧州では英国がECからの離脱作業に入り,EC内各国でも離脱活動が活発化しつつあるとか・・・
これは,広大な自由貿易圏を前提にし,量産効果を狙って数カ所の巨大工場から全世界に向けて商品を届けると言う戦略の見直しを迫る動きであります。
弊社の表看板 『Jコスト論』に従えば,大量生産工場内では原価は安くなる場合もあるが,お客様との距離が遠くなるために,運賃等の諸経費が嵩むだけでなく,商品のLead-Time,言い換えれば資金の回転が遅くなってしまいかえって不利であることが導かれます。
又,弊社のもう一つの表看板の 『本流トヨタ方式』にある 『共存共栄』の哲学からは,地域の人を雇い,地域のSupplierから部品を買い,地域に納税する事や,問題が生じたとき当意即妙で対応する等々,自律分散型の工場となり,その地域に無くてはならない存在として認められる事こそが,企業の継続の鍵であると示唆しています。
つまり,米英の昨今の動きは弊社の目指す方向に対してはむしろ 順風と言えます。
此の肝となるのが 『第一線の管理者の養成』にあります。
弊社は昨年に続き今年も,中国では監視カメラの大手Dahua社,国内では最大手K社の 『管理者による工場改革』のお手伝いを中心において取り組んで参ります。新規のご要望があれば改革のお手伝いに参じたいと思いますが,余力は限りがあり,全ての皆様のご要望にはお応えできませんますので,本年はこのWebサイトに
というコラムを設け毎月当社の改革のノウハウの一端を御説明することにしました。
その中では,良い例も悪い例も主として中国企業の実例を引用してお話しして行きますが,何よりの目玉は,
日本企業の中で現在進行中の『Jコスト改革』の実例として伊牟田社長,鈴木工場長を中心として全社一丸となって今日も進めているナブテスコ社鉄道カンパニーの活動事例を同社の協力を得て紹介できることにあります。
毎月楽しみにして頂くとともに,是非,友人にもご紹介下さい。
註:伊牟田・鈴木の両氏には弊社より『Jコスト改善士』の称号を贈呈しています。
業務内容ページの
8.『Jコスト改善士』の資格審査・登録・管理業務欄の「Jコスト改善士」の称号贈呈をご参照下さい。